Which Pump Is Used For High Pressure?
For high-pressure applications, several types of pumps are commonly used, depending on the specific requirements of the system.
Positive Displacement Pumps: These pumps are often used for high-pressure applications because they can generate high pressures by trapping a fixed amount of fluid and forcing it into the discharge pipe. Examples include:
Gear Pumps: Use rotating gears to move fluid.
Diaphragm Pumps: Use a diaphragm to create a vacuum and draw fluid in.
Piston Pumps: Use a piston to create pressure and move fluid.
Centrifugal Pumps: While typically used for lower pressure applications, certain designs of centrifugal pumps can be configured for high-pressure applications, especially multi-stage centrifugal pumps, which have multiple impellers to increase pressure.
High-Pressure Water Pumps: Specifically designed for applications like pressure washing, firefighting, and industrial processes, these pumps can handle very high pressures.
Hydraulic Pumps: Used in hydraulic systems, these pumps can generate very high pressures to operate machinery and equipment.
Plunger Pumps: These are a type of positive displacement pump that can achieve very high pressures, often used in applications like water jet cutting and pressure washing.
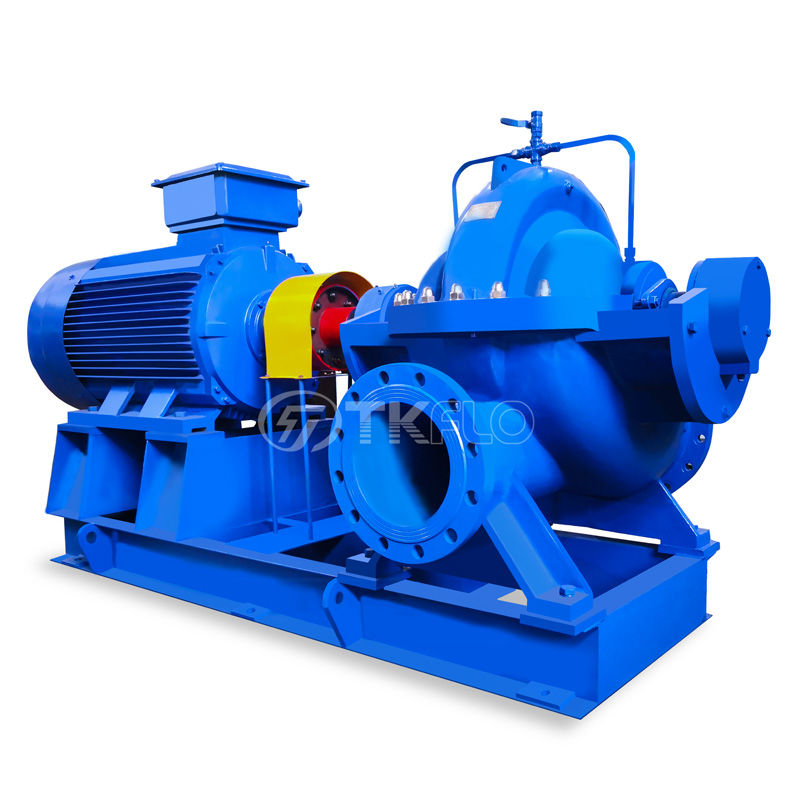
Diameter | DN 80-800 mm |
Capacity | no more than 11600m3/h |
Head | no more than 200m |
Liquid Temperature | up to105 ºC |
1.Compact structure nice appearance, good stability and easy installation.
2.Stable running the optimally designed double-suction impeller makes the axial force reduced to the minimum and has a blade-style of very excellent hydraulic performance, both internal surface of the pump casing and the impeller's surface, being precisely cast, are extremely smooth and have a notable performance vapor corrosion resisting and a high efficiency.
3. The Split Casing Centrifugal Pump case is double volute structured, which greatly reduces radial force, lightens bearing's load and long bearing's service life.
4.Bearing use SKF and NSK bearings to guarantee a stable running, low noise and long duration.
5.Shaft seal use BURGMANN mechanical or stuffing seal to ensure a 8000h non-leak running.
6 . Flange standard: GB, HG, DIN, ANSI standard, according to your requirements
What Is The Difference Between a High Pressure Pump And a Normal Pump?
Pressure Rating:
High-Pressure Pump: Designed to operate at significantly higher pressures, often exceeding 1000 psi (pounds per square inch) or more, depending on the application.
Normal Pump: Typically operates at lower pressures, usually below 1000 psi, suitable for general fluid transfer and circulation.
Design and Construction:
High-Pressure Pump: Built with stronger materials and components to withstand the increased stress and wear associated with high-pressure operation. This may include reinforced casings, specialized seals, and robust impellers or pistons.
Normal Pump: Constructed with standard materials that are adequate for lower pressure applications, which may not be able to handle the stresses of high-pressure operation.
Flow Rate:
High-Pressure Pump: Often designed to provide a lower flow rate at high pressure, as the focus is on generating pressure rather than moving large volumes of fluid.
Normal Pump: Generally designed for higher flow rates at lower pressures, making them suitable for applications like water supply and circulation.
Applications:
High-Pressure Pump: Commonly used in applications such as water jet cutting, pressure washing, hydraulic systems, and industrial processes that require precise and powerful fluid delivery.
Normal Pump: Used in everyday applications like irrigation, HVAC systems, and general fluid transfer where high pressure is not a critical requirement.
High Pressure Or High-Volume?
High-pressure pumps are used in applications requiring forceful fluid delivery, while high-volume pumps are used in scenarios where large quantities of fluid need to be moved quickly.
High Pressure
Definition: High pressure refers to the force exerted by the fluid per unit area, typically measured in psi (pounds per square inch) or bar. High-pressure pumps are designed to generate and maintain high pressure in a system.
Applications: High-pressure systems are often used in applications that require the fluid to overcome significant resistance, such as water jet cutting, hydraulic systems, and pressure washing.
Flow Rate: High-pressure pumps may have lower flow rates because their primary function is to generate pressure rather than move large volumes of fluid quickly.
High Volume
Definition: High volume refers to the amount of fluid that can be moved or delivered over a specific period, usually measured in gallons per minute (GPM) or liters per minute (LPM). High-volume pumps are designed to move large quantities of fluid efficiently.
Applications: High-volume systems are commonly used in applications such as irrigation, water supply, and cooling systems, where the goal is to circulate or transfer large amounts of fluid.
Pressure: High-volume pumps may operate at lower pressures, as their design focuses on maximizing flow rather than generating high pressure.
Booster Pump Vs High Pressure Pump
Booster Pump
Purpose: A booster pump is designed to increase the pressure of a fluid in a system, typically to improve water flow in applications such as domestic water supply, irrigation, or fire protection systems. It is often used to boost the pressure of an existing system rather than generate extremely high pressures.
Pressure Range: Booster pumps usually operate at moderate pressures, often in the range of 30 to 100 psi, depending on the application. They are not typically designed for very high-pressure applications.
Flow Rate: Booster pumps are generally designed to provide a higher flow rate at the increased pressure, making them suitable for applications where a consistent and adequate water supply is needed.
Design: They can be centrifugal or positive displacement pumps, depending on the specific requirements of the application.
High-Pressure Pump
Purpose: A high-pressure pump is specifically designed to generate and maintain high pressures, often exceeding 1000 psi or more. These pumps are used in applications that require significant force to move fluids, such as water jet cutting, pressure washing, and hydraulic systems.
Pressure Range: High-pressure pumps are built to handle very high pressures and are often used in industrial or specialized applications where high pressure is critical.
Flow Rate: High-pressure pumps may have lower flow rates compared to booster pumps, as their primary function is to generate pressure rather than move large volumes of fluid quickly.
Design: High-pressure pumps are typically constructed with robust materials and components to withstand the stresses associated with high-pressure operation. They can be positive displacement pumps (like piston or diaphragm pumps) or multi-stage centrifugal pumps.
Post time: Dec-13-2024